News
ONE STOP METAL CUTTING SOLUTION FOR HIGH SPEED CIRCUALR SAW MACHINE + FACING MACHINE + CHAMFERING M
11 Jan February 2025 | LionNord
How to make a automatic high speed circular saw machine +facing machine + chamfering machine line ?
Introduction of circular saw machine
4.1 Name, model and use of the equipment:
1, equipment name: automatic high-speed metal circular saw machine
2. Model of the equipment: 50NC
3. Purpose: to meet the requirements of round steel fixing and high-speed sawing proposed by Party A.
4. Process object: round steel φ 33- φ 33mm
5. Workpiece material: 20MnCrS5
6, blank material length: 6000mm
7. Length after underfeeding: 200-807mm
4.2 Main components of the equipment:
automatic high-speed metal circular saw machine for the conventional machine tool produced by our company, mainly composed of machine bed body, power head part, feeding system, clamping device, hydraulic system, electrical system, spray cooling system, automatic lubrication system, saw blade cleaning device, automatic feeding mechanism, feeding frame, front discharge frame and other parts.
(1) Machine bed body: the main body of the bed is cast by gray cast iron. After high temperature tempering and aging treatment, the casting has no inclusion, bubbles and cracks and other defects, has the characteristics of good overall rigidity, high strength, impact resistance, small deformation, can greatly improve the overall rigidity and saw stability of the machine tool.
(2) Power head: the gear box is made of grey cast iron, with high strength and impact resistance. The transmission gear made of high-performance gear material passes through special heat treatment and precision grinding to ensure the transmission stability and high transmission efficiency. All bearings use imported high precision, high strength bearings, so that the whole gearbox running noise, stable, reliable transmission performance, workpiece saw cutting precision, no burr. The spindle adopts advanced structure, which can be suitable for the installation and use of the same type of saw blade in China and abroad. It is more reasonable than the existing domestic structure, which is widely used in structure and installation, and greatly enhances the impact resistance of the spindle. The magnetic powder brake imported from Taiwan realizes the gear gap compensation function, realizes the zero clearance gear transmission in the saw process, makes the saw process more stable and prevents the saw blade from shaking. The use of the unique saw blade stability system can greatly improve the rigidity of the clamped round saw blade, reduce the vibration and swing of the saw blade, so that the service life of the saw blade is further improved, and the saw accuracy is reliably guaranteed.
(3) Feed system: the ball rod is driven by the servo motor for parallel strong feed, to cut off the clamped workpiece with high precision. The guide rail is equipped with Taiwan silver overloading linear guide rail, which can adapt to the sawing of materials with high tensile strength.
(4) Clamping device: it is composed of two groups of horizontal and vertical hydraulic clamping devices. The clamping jaw material is made of alloy steel and the hardness reaches HRC 52 ° after quenching. The front and rear fixtures can be clamped and loosened at the same time, which can be adjusted according to the clamping force of the required workpiece to ensure the stability of the saw process.
(5) Hydraulic system: composed of oil tank, concentration block, hydraulic pump, hydraulic components, execution components, etc., it adopts international famous brand hydraulic parts, low failure rate, reliable performance, stable and reliable to achieve a variety of program action. The pipe distribution specification of the hydraulic system is convenient for equipment maintenance and disassembly, and the moving parts are equipped with drag chain for protection. The hydraulic system is designed as a centralized hydraulic station. The hydraulic system has automatic shutdown and alarm function.
(6) Electrical system: composed of electrical cabinet, touch screen, press button, PLC, motor, contactor, relay, heat exchanger, switch and auxiliary components, etc. The machine tool can realize the whole process of numerical control, that is, in addition to the bundle lifting and removal of packaging is manual operation, from automatic dialing to saw cutting completed. The machine tool adopts Ethernet communication, and the database has reserved access interface to facilitate data extraction.
(7) Spray cooling system: using imported brand spray cooling lubrication system, the system uses environmental protection cutting oil for accurate metering of microspray method. The carefully designed nozzle spray efficient cutting oil to the saw tooth to reduce the generation of cutting heat. When the nozzle spray efficient cutting oil to both sides of the saw blade at the same time, it can not only improve the production efficiency, reduce the production cost, prevent environmental pollution, but also improve the incision quality and prolong the service life of the saw blade.
(8) Automatic lubrication system: it has an independent closed lubrication system to lubricate the mechanical transmission parts such as bearings and slides. The lubrication mode is automatic lubrication, and the lubrication is once every fixed time under the premise of ensuring the lubrication effect, and has low liquid level lubrication alarm.
(9) Saw blade cleaning device: a saw blade cleaning device is provided in the head part of the saw machine to clean the steel chips attached to the saw tooth part when the saw cuts, avoid the secondary cutting of the saw blade and improve the service life of the saw blade.
(1 0) Automatic feeding mechanism: automatic feeding adopts AC servo control of high precision ball wire rod + optical shaft guide column, so that the accuracy of feeding is reliably guaranteed. The force of the clamped rod material is enough, and there is no skid, stop and other phenomena. The feeding mechanism feeding according to the set length of the system, and sawing after clamping. The equipment is equipped with photoelectric type detection switch, which has the automatic detection function of the front position of the material.
(1 1) feeding frame: mainly composed of loading frame, turning mechanism, conveying roller, etc. The table is used to put raw materials to be cut, the bearing frame is used to put raw materials to be cut in bundles, and the length of the frame can be placed 4-6 meters of raw materials. The feeding mechanism will turn the raw materials onto the main automatic feeding mechanism, which will cut the feeding mechanism according to the set length of the system. The equipment is equipped with photoelectric type detection switch, which has the automatic detection function of the front position of the material. In order to solve the defects of the front end of raw materials. The front position error of the materials within 200mm can be produced normally.
(12) Front discharging frame: composed of discharging rack, chain conveyor belt, retaining mechanism and push mechanism. When sawing the head and tail material, the retaining mechanism is open, and the head and tail material is transported from the chain conveyor belt to the tail drop. When the saw is cut into material, the retaining mechanism is closed. After the finished material is cut off, the switch is sent from the chain conveyor belt to the retaining mechanism to detect the signal, and the push mechanism pushes out the finished material from the side and falls into the chamfer machine.
Introduction of the chamfer machining function
Name, model and use of the equipment:
1, equipment name: automatic double-head chamfer
2. Equipment model: LJDJ-D60-800L
3, use: to meet the customers requirements of round pipe fixing and high speed cutting.
4. Process object: φ 20- φ 60mm round tube / rod material.
5, workpiece material: 20,45,25 Mn, Q345D
6. Processing length: 200-800mm
8. Processing mode: mode 1 —— Automatic cycle mode
Mode 2 —— Manual single-pass mode
Introduction of the machining function of double-head milling end surface
Name, model and use of the equipment:
1, equipment name: automatic double-head milling end face host
2. Equipment model: LJPX-D60-800L
3, Use: to meet the customers requirements of round pipe fixing and high speed cutting.
4. Process object: φ 25- φ 55mm round tube / rod material.
5, workpiece material: 20,45,25 Mn, Q345D
6. Processing length: 165-850mm
8. Processing mode: mode 1 —— Automatic cycle mode
Mode 2 —— Manual single-pass mode
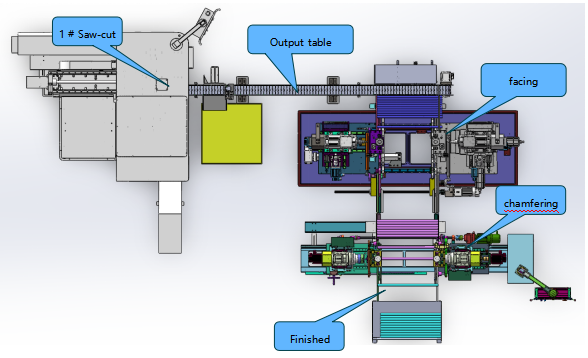
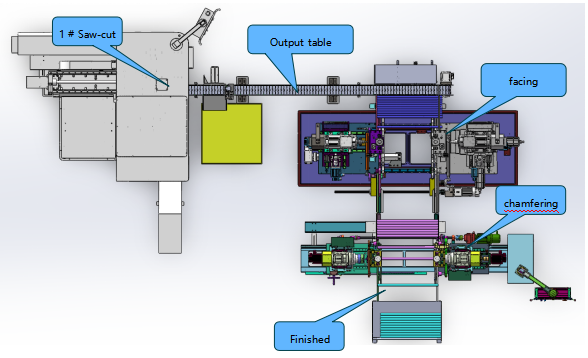